|
|
|
|
- IngenieriaPlastica.Com - Entrevistas |
RAUL MADEIRA;
LA INVERSION EN MOLDES NUNCA PUEDE SER UNA AVENTURA
Volver a Entrevistas
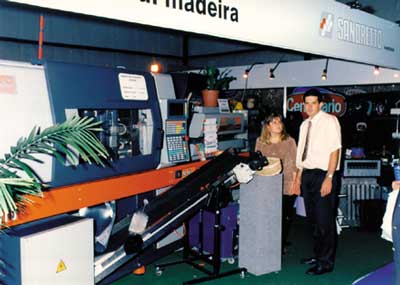
¿Cuándo comienza actividades Raúl Madeira?
En el año 1957, 1º de enero, dedicándose a la fabricación de matricería para corte, estampado y corte de chapa, y moldes para plásticos. Al mismo tiempo surge también la fabricación de moldes para goma, vidrio y para termoformado de envasado automático. Se empieza la fabricación de elementos para extrusión, como cabezales y de todas esas actividades la que más se despegó es la de moldes para plásticos. Durante muchos años prácticamente el 90% de la actividad fue la fabricación exclusiva de moldes, pero ahora, a tomado mucho auge los mecanizados industriales. Hoy en día es la principal actividad de la empresa, contamos con equipos de avanzada en cuanto a computación, ya que nuestro equipamiento y soporte tecnológico consta con un poderoso sistema de C.A.D. (diseño asistido por computadora) complementado con el sistema de C.A.M. (mecanizados asistidos por computadoras) para programación rápida de nuestros equipos de mecanizado por control numérico, partiendo no sólo del diseño sino también del digitalizado(escaneado tridimensional) de moldes o prototipos. Esos mismos equipos también los usamos para la parte de fabricación de repuestos en el sector metalúrgico, levas, repuestos aeronáuticos, (este año vamos a ser homologados como primer taller habilitado para fabricar repuestos aeronáuticos) y dentro de lo que es la parte de moldes, fundamentalmente los que son para inyección y soplado. En este momento lo que esta en auge es la parte de moldes para soplado de PET. Estamos fabricando muchos, incluso para el exterior y moldes para prensado e inyección de silicona que también es poco común acá en el País.
¿Exportan?
Nuestros mercados tradicionalmente eran 50 % exportación 50 % fabricación nacional y esa proporción si bien en la parte nacional ha disminuido, se mantiene el nivel por el hecho que se está trabajando mucho indirectamente para empresas que están exportando. Somos exportadores tradicionales de matricería, básicamente para diversas industrias de países como Argentina, Brasil, Chile y Paraguay. Además estamos exportando para empresas que están instaladas en Zona Franca.
¿Con respecto a venta de maquinarias?
En el Uruguay tenemos la representación de la firma Sandretto de Italia, una de las principales marcas mundiales de máquinas inyectoras. Hace ya 27 años que introdujimos la marca y bueno se sigue vendiendo a un ritmo mas o menos sostenido con una fuerte competencia de máquinas de Oriente. Pero así mismo es una marca que se respeta mucho. Los repuestos son originales de fabrica, y no hay problema con el costo ya que Sandretto se fabrica también en Brasil, siendo el abastecimiento directo de San Pablo y en pocas horas.
¿Cómo es el proceso para el diseño de un molde?
La fabricación de los moldes es cara, por eso la inversión que el realice en el molde nunca puede ser una aventura. Para ello primero le brindamos al cliente la fabricación de los prototipos por estereolitografía. Con este proceso para todo diseño de las piezas, te permite darle al cliente un servicio completo, es decir el te trae una idea y con ese boceto inicial se fabrica un diseño, luego se realiza el modelo sólido virtual (CAD), logrando un prototipo y sobre la base de eso se fabrica el molde. La garantía para el cliente es que el tiene antes el prototipo.
¿Cómo se llama ese sistema?
- Estereolitografía, proceso que a través de una resina fotosensible al rayo láser que cargando el dibujo del sólido en 3d en la máquina, genera a través de ese dibujo la pieza en resina. Para el cliente la seguridad de tener la pieza antes de empezar a hacer el molde, antes de hacer la inversión. Y para el matricero la seguridad de que va derecho a hacer lo que el cliente quiere y no tener después que modificar las matrices. Es una doble garantía, la inversión de un molde es cara, pero el costo de este proceso tiene un porcentaje que no incide y da una muy buena seguridad y tranquilidad al inversor.
¿Algún nuevo proyecto de Raúl Madeira?
Bueno se han incorporado máquinas de electroerosión, de penetración por control numérico. Esto permite ahorros muy significativos en lo que refiere al cambio de electrodos, es decir, teniendo por ejemplo un molde que es de varias cavidades con un mismo electrodo la máquina comienza a hacer el trabajo de erosión en una cavidad, cuando la termina pasa automáticamente a la otra y así sucesivamente, con el intercambio incluso de electrodo, poniendo los de desbaste y los electrodos de terminación. Es un proceso mucho más preciso, no hay errores, la máquina trabaja a la centésima de milímetro perfectamente, y trabaja las 24 hs. sin parar. Se ahorra mucha mano de obra y el proceso es mucho mejor y más rápido.
¿Cuándo comienza Plamet?
Hace más de 25 años, había iniciado sus actividades como fábrica de artículos de escritorio, donde existían balancines para corte y estampado de chapa. En el año 82 se anexa la parte de plásticos. A partir de ese momento se desarrolla lo que son los termoplásticos de ingeniería. Es decir se trabaja mucho el PVC rígido, mucho policarbonato, con cargas, de fibra de vidrio, micro esfera de vidrio, amianto, retardante de llama, se fabrica piezas en resinas acetálicas, con cargas, poliamida con fibra de vidrio. Y mucho en ABS.
Todos estos productos requieren de una calidad técnica....
- Exacto. Participamos en el proyecto del desarrollo para los radiadores de una marca importante de automóviles, donde nosotros suministramos los cabezales de los radiadores en poliamida con fibra de vidrio, material de Rodhia, Rhone Poulenc Francia, que en este caso viene de Brasil. También estamos abocados a un proyecto interesante, donde fabricamos las derivaciones para redes de alta tensión, piezas que son en policarbonato transparente que después en el proceso de cerrado las complementan con una resina que es la que aísla el empalme que se hace, es un proceso subterráneo. Hacemos la inyección de la carcaza, una carcaza con forma de tortuga. Muy importante es la parte de resinas acetálicas que se hacen engranajes que son para uso industrial, cajas de velocidades, se hace mucho PVC rígido. Cabezales para intercambiadores de resina, de intercambio iónico para purificadores de agua, se hacen también unos acoples de PVC que tienen la característica de que tienen que soportar mucha presión de servicio, ya que se usa para los empalmes que van en las líneas de cañería, tubería que llevan bombas sumergibles.
¿Alguna proyección especial?
Realizar los proyectos de exportación en que hay tecnología aplicada, muy buen equipamiento, muy buena maquinaria, la idea es justamente captar los mercados que sean ávidos de ese tipo de servicio.
Volver a Entrevistas
|
|
|